Work uniforms can establish an impressive image for your company and can help to protect workers. Uniform workwear can reflect a good company culture, standardize management, and improve the visibility of the company. Whatever your reasons are for choosing uniforms in your company, you should consider a few things before making any major purchases or agreements. These options can help you save budget and increase the safety and security needs for your employees.
1. who will wear uniform
Work uniforms should be symbolic, and different positions should have different work clothes, so that the type of work can be clearly distinguished and the overall image of the company can be improved. For example, office workers wear black suits and white shirts; technicians wear blue overalls; dangerous jobs wear orange and reflective overalls; hotel chefs wear white chef clothes.
2. what style you need
When we determine which job position requires custom work uniforms, we can increase the function of the workwear according to the special requirements of the position. For example, doctors often use pens and stethoscopes. Is it possible to add extra small pocket on the chest and arms, and add 2 straps under the shoulder on to hold the stethoscope? Another example, Because the chef works in a high temperature environment an oil, the chef uniforms are in cardigan design, front in double-layer insulation and avoids being scalded by high-temperature oil, and the back yoke and armhole area are replaced by mesh, this way it will be more comfortable and breathable. If you need some reference style of work uniforms, please feel free to contact us, we are pleasure to send our product catalog.
3. what fabric is right
In theory, different working environment has different requirement for fabric, It is necessary to choose the right fabrics. If you have requirements, you need to indicate the ingredients, gram weight, color fastness, etc. We have put together a form for your reference. Of course, if you need to customize fabrics strictly according to the requirements, you need a relatively large quantity, generally more than 10,000 meters, if the quantity is not enough, purchasing existing fabrics is also a good choice.
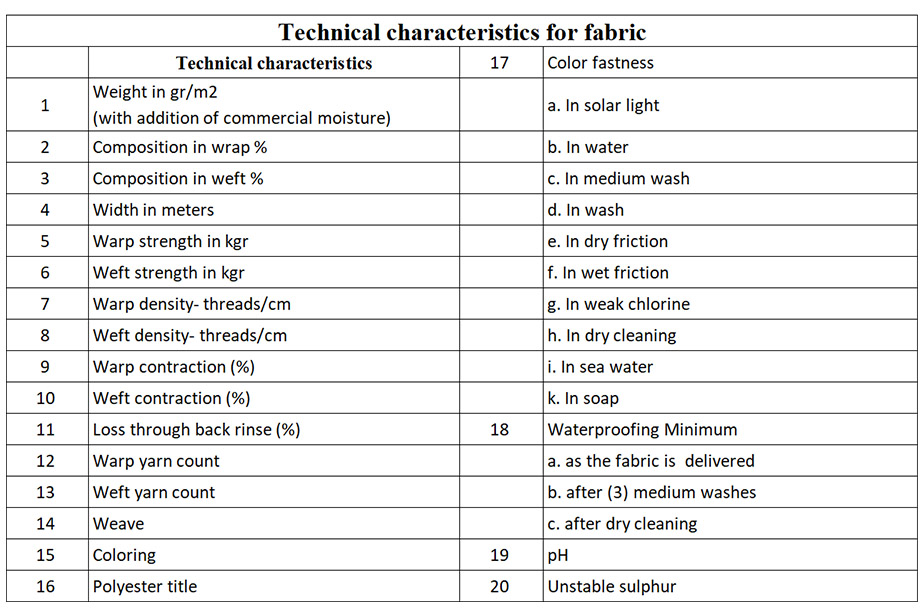
4. what size meet your market
Select the appropriate size meet your market. This is important, every market size is different. If you have samples, it will be better to send the samples to your supplier, if you don’t have samples need to give specifications for several key parts, like chest, waist, bottom and length. In this way, the sample from supplier can be right fitting, you can get the right size measurement, it will be good to sell to your end users. If you don’t have size measurement, you can contact us, we have 10 years experience in producing workwear and selling to the United States, Australia, Europe and the Middle East, we can provide you with the best suggestion and solution.
5. how many uniforms you need to buy
This is a very necessary point. Uniform manufacturers calculate a reasonable price according to the quantity. Usually they will have a MOQ for the custom uniforms, it’s various from different supplier, the lowest usually start from 100 pieces. However, The price of 100 pieces is much higher than the price of 10,000 pieces. As we all know that, the more you buy the more discount you can get.
6. how much you need for production
Some supplier will request a Minimum US$ 1000 for an order, some will ask a minimum 100 pieces, cost is different in designs, a simple t shirt will be much cheaper than a jacket. In most cases, you need to pay a 30% deposit to the uniform manufacturer to start the order. They will for purchasing fabrics and accessories, and the remaining 70% will be paid once goods ready. Some companies need to provide a 50% deposit, usually it will take about 30 days in production. So you can prepare the half to start, rest in a month.
7. when will get the uniform
In order to get your uniforms on time, it is necessary to give enough time for production and logistics, it is better to make a reasonable purchasing plan. It will take about 7 days to make samples with heyday, including purchasing fabrics and accessories, design and pattern, cut and sew and iron. 5-10 days to delivery to you by courier. Due to Covid, it may take longer. For production usually about 30 days depending on style and quantity. We can produce about 30,000 pieces uniforms in a month. However, if the fabric request not have stock, need to custom order the fabric, then custom uniform delivery time will need extra time for making fabric, usually about 15 days on custom fabric.
8. which way is the best to send the uniform
The shipping method you use depends on how much you can pay for shipping and when you received it. It can be divided into the following 4 ways: air, sea, courier and train. By air and courier, it’s fast but cost high, mostly take about 7-10 days. if not in hurry, sea and train or truck are the good choices. The price is much cheaper than by air, which can effectively reduce costs and improve Product competitiveness.
The End
If you have any inquiry about uniforms, please feel free to contact us.